Technology of GD.findi
- Home
- /
- Technologies
- /
- Technology of GD.findi
Innovating Your Process Design Through GD.findi
It is difficult to make changes in the active production sites, such as modifying the in-plant logistics and shifting the established production line. Therefore, making changes, or “KAIZEN”, in the production process preparation stage is critical and more effective for the company.
Process planners use production simulators to evaluate certain aspects such as “process design” and ‘factory layout design’ that are crucial for optimal production output. However, the current conventional simulator technologies possess many problems.
For example, difficulties in the operation and use extremely time-consuming, and high cost, are notable problems experienced by those using the simulation programs. In addition, companies that employed programmers to design the process and production line layout had to delay their production due to laborious design work. Even in major manufacturing companies, there were cases where they had to start their production line since the process simulation was consuming too much time.
Although the usefulness and effectiveness of the process simulation is known by companies, it is not standardized by the industry to use the simulation program.
More so, companies that customized the program have considered it an obsolete program.
Aside from raising the problems associated with the conventional simulation program, the fundamental problem with the simulation programs is that it requires professional simulation programmers to input data. Process planners are not specialized in IT programming, thus have to rely on simulation programmers. However, the simulation programmers themselves are not familiar with the production site and do not accurately portray simulations that “KAIZEN” the production methods.
Therefore, the conceptual differences experienced by the process planners and simulation programmers led to additional problems that caused laborious redesigning of the floor plan in addition to accruing unnecessary loss of time.
Fixing the parameter setting was not enough to overcome to the problems and required the simulation programmers to modify the program.
The modification of the simulation program may take days to several weeks, causing a standstill of the production. As a result, the company had to forfeit the cost from production loss and the fee for modifying the simulation program.
Therefore, to overcome the problems experienced in the industry, LEXER proposed to change the simulation program. LEXER developed a new technology for the production assembly site based on a concept that differs from the conventional production simulation programs. LEXER Research’s approach to revolutionizing the simulation program is to create a program that is easy to use for all personnel involved with the production operation (ex. process planners, operation managers, etc.). The user-friendly software does not require professional programmers to operate the system. LEXER’s program will allow the users to customize the process plan simulator based on their own experience, knowledge, and creativity. With the user’s skills and LEXER’s simulation program, users can improve their operational efficiency and production value. Users can also explore and expand on their ideas with this program, which will allow the process planners to further develop their organization and leadership skills. Process planners can utilize LEXER’s Powering Process Design as a powerful management tool.
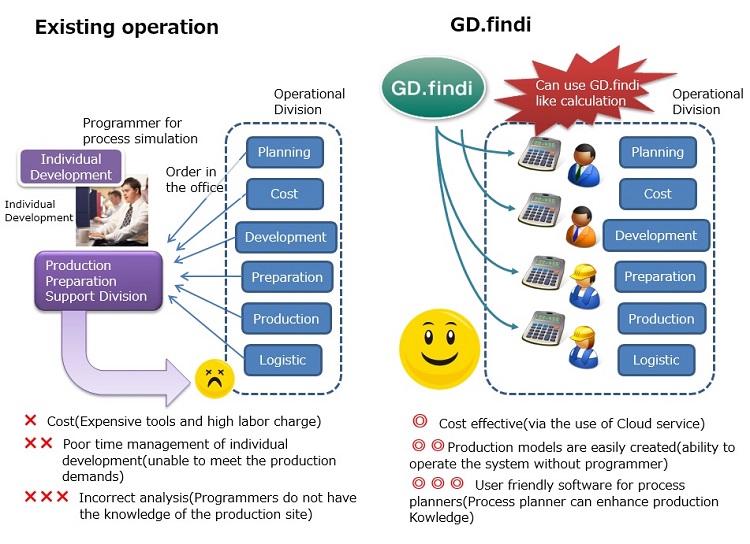
Improve Your Process Design!
In the ‘Our Technology’ section, we explained how our program can revolutionize your process planning. In this section, we will explain how your daily process planning can be simplified with the GD.findi simulation program. The greatest feature of the program is that it does not require extensive programming skills. The conventional process plan simulation needs programming experts to layout the plan. However, as the mixed model production and automation process complicated the modern process plan, the programming experts were not able to sufficiently utilize their skills. In addition, with a demand for shortened production life, it is difficult for the companies to make any changes to their production process. Therefore, companies must plan well to achieve maximum production output from the start of their production process. This can only be achieved by creating a complete and faultless process plan. Process planners, operation managers, and other personnel in charge of managing the operation can easily create the process design. This is because the program functions like a ‘scientific calculator’. GD.findi’s High-Resolution Process Design can help users with their daily process planning. The multi-functional calculation program lets the users create their process design in a shorter amount of time. In addition, users are able to visualize vivid images of their designing due to GD.findi program’s remarkable ability to resolve empirical values associated with logistics and organizational changes. Revolutionize your process design with GD.findi’s power tool, the High-Resolution Process Design!
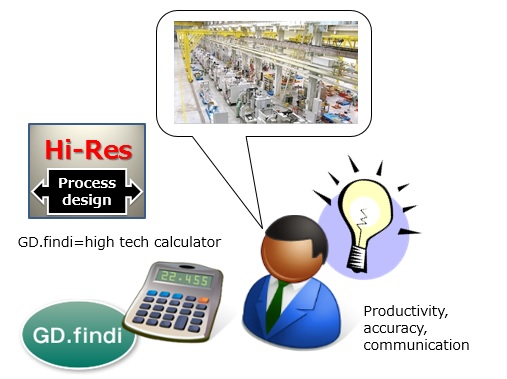
In this section highlights the power tool characteristics that GD.findi based their research:
1) Planning of the production line balancing
2) Design the floor plan according to the factory layout and equipment used
3) Production line balancing that factors in step-by-step process and interbay transfer time
4) Exhibit the dynamics involved in product changeover
5) Ensure the stock for the production line
6) Aid in deciding the interbay transfer and product logistics
7) Forming the team members and organizing their tasks
(The throughput time stated here is for the time needed for the production process. It does not include interbay transfer and its set up time.)
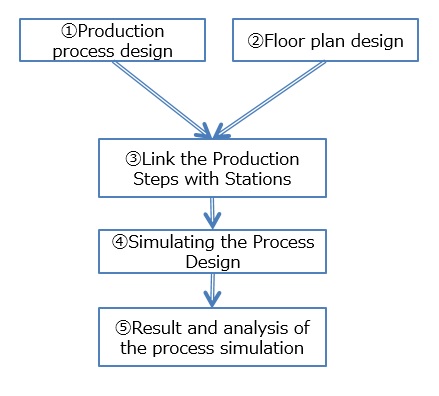
①Production Process Design: Confirm the over-all design.
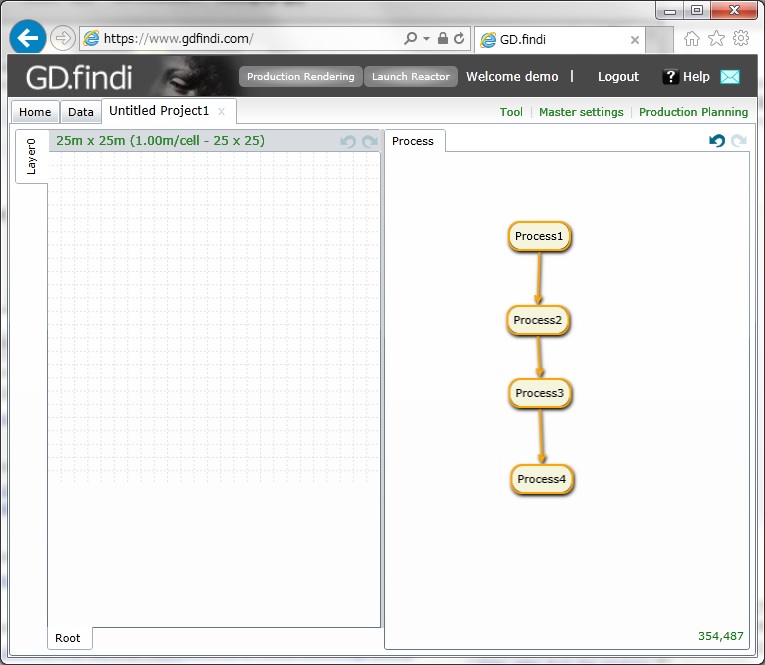
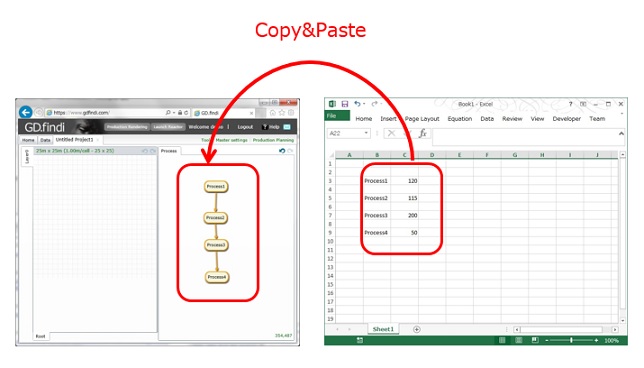
➁Floor Plan Design
Floor Plan Design : Can easily design the factory layout by placing its image to the background. Afterwards, place the stations and logistics pathway.
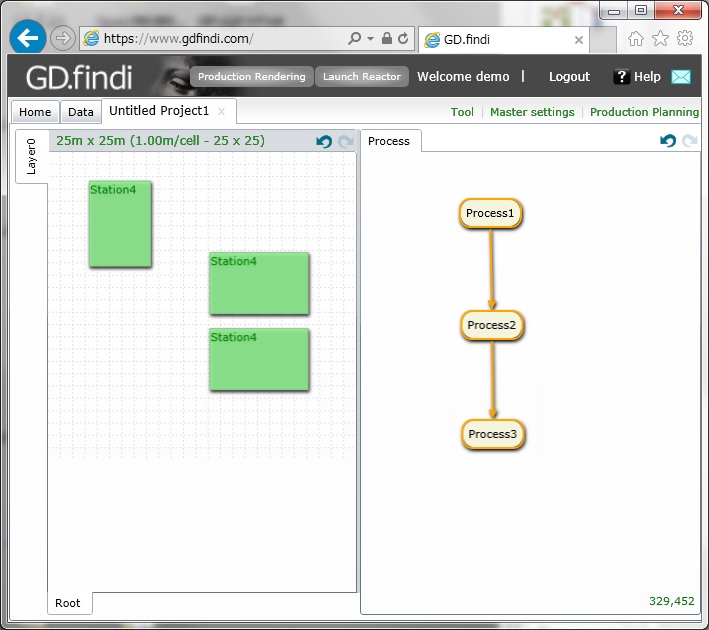
③Link the Production Steps with Stations
GD.findi will correlate the production process step and floor plan. Each production step is dragged and dropped to the floor plan’s station. The assigned station will function as a production line and the program will adjust the production line balance.
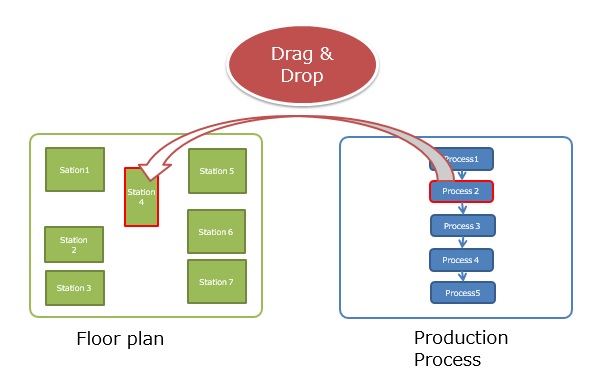
Step 3 linked the production step with the corresponding stations. By looking at the station’s product load, one can confirm the line balance of the overall production line. At this point the line balance is at a stationary condition, therefore the interbay transfer and its setup time is not included. On the other hand, if there is a loading problem within the line balance, then one can make adjustments of the production step by changing the station to maintain the balance.
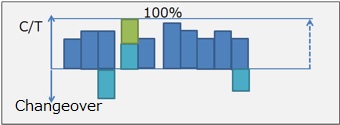
At this point, the static state of the production process can be simulated by programs such as Excel. However, using the GD.findi program will allow the systematic management of the production process and process design. Dynamic movements (loading/unloading, product changeover, logistics, stocks, employee management) are impossible to simulate by Excel, yet they are essential for creating a perfect process design. We will explain how this can be done with GD.findi.
④Simulating Your Process Design
Users can visualize the dynamic element of the process design through the GD.findi simulation program. In order to conduct the simulation, it requires a realistic process design which includes fine details such the production lot and input order. The program’s production setting panel allows customizing the production plan. After the customization, the production simulation set up is complete. The high speed production simulation can be viewed (press the ‘Production Rendering’ button) through the simulation cloud service. The ‘Production Rendering’ of the GD.findi program calculates the given data; thus letting the users visualize the product and employee flow.
⑤Result and Analysis of the Process Simulation
Once the production rendering is complete, users can visualize the product and employee flow. They can also see the detailed simulation (such as how many products are available at a certain time) by maneuvering the production dashboard. In addition, users can even visualize the time required for the interbay transfer and product changeover, allowing a highly accurate production line balancing. If users find a problem with the line balancing, they are able to make changes to the production step via station reassignment. GD.findi is a simulation program that also functions as a support tool for the process design. GD.findi’s flow diagram makes it easy to see the overall product flow. It is separated into product flow (top to bottom) and time (left to right), and users can see the changes in production lot (ex. Bottlenecking of the products) through these two factors. The program can efficiently resolve a variety of complicated production plans and offer accurate analysis faster than the conventional simulation programs.
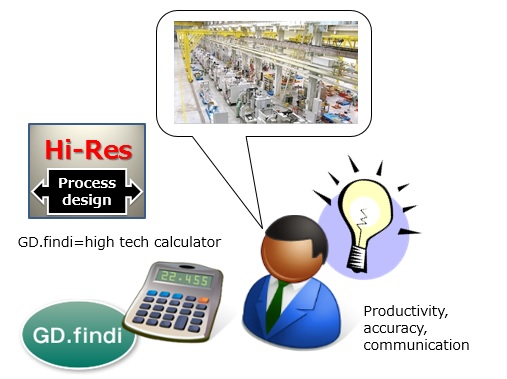
Independent Data Architecture
One of GD.findi’s main qualities is the floor plan and production process work separately and independently from each other. Although floor plan and production process are closely tied together to produce products, they do not have a strong correlation when a production plan is in its early stage. When a product is designed, the components of the product, production method, and its instruction manual must be established in order to start the production process. Production process is therefore strongly associated with product design compared to the floor plan. When designing the production process, the productivity and cost effectiveness are taken into consideration. With this in mind, users can create various floor plans and production processes to maximize their production. Thus, having the two factors independent from each other allows greater flexibility in designing and simulating the ‘data architecture’ that structures your plan. (LEXER’s patented technology)
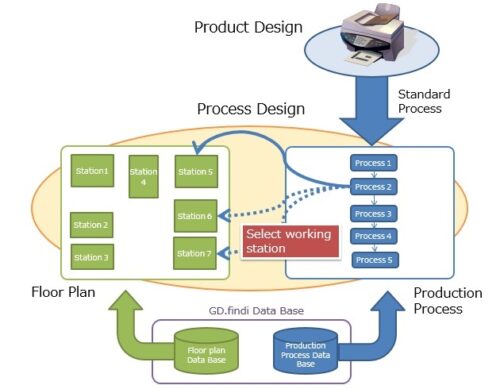
The conventional production simulator does not support this technical concept. Most standard simulators function as discrete, individual simulation where the product flow is precisely conditioned at each station (refer to diagram). However, the station’s process and how the product flows through it is a limiting factor when the user is running the simulation. One, the program that orders the product flow (line) must be rewritten when the user needs to make changes to the flow. This requires a program specialist and it can be time consuming. Moreover, the major problem of conditioning the product flow through the station is that it heavily effects the operation of the simulation. Instead of defining the production flow process, it is functioning as ‘defining the condition of the product flow and verifying the processv. The objective of a process design is to determine how the product flows and to properly assign the station to perform its function. It is difficult to define the process with the conventional simulators, and as a result, users must verify if the process is meeting the purpose of its design. To overcome this problem, LEXER created GD.findi.
GD.findi overcomes conventional simulation's problems.
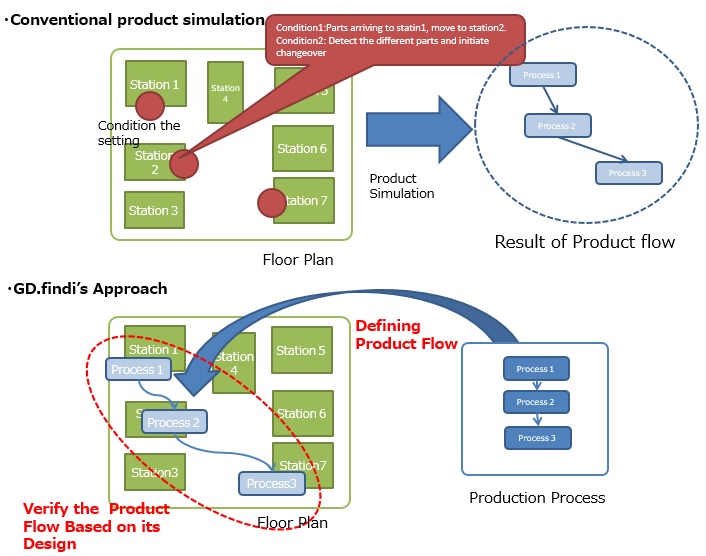
How is the independently defined floor plan and production process linked together? GD.findi allows this by selecting the production process and simply ‘drag & drop’ to assign it to the station in the floor plan. The station can be assigned single to multiple functions and the linked information is stored in GD.findi’s database. Afterwards, the user can set up their production plan to activate the production simulation and view it to verify the product flow.
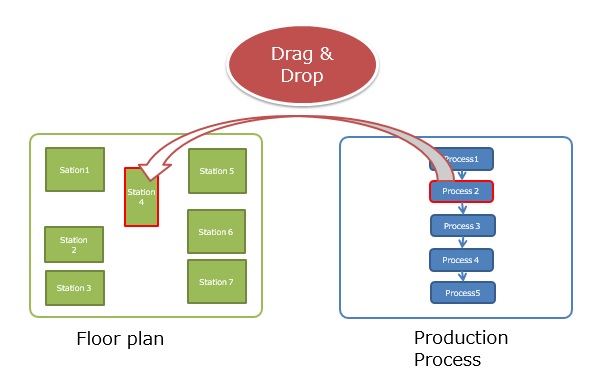
Intelligent Control of the Logistic Activities and Management of the Employees
GD.findi’s concept, approach, and data architecture was introduced to the users to help them understand the program’s fundamentals. We will now explain how GD.findi’s sensitive analysis function can support the challenges faced by the process designers. In process designing, the static state of the production process can be simulated by programs such as Excel. Dynamic movements (loading/unloading, product changeover, logistics, stocks, employee management) are impossible to simulate by Excel, yet they are essential for creating a perfect process design. Designers that did not utilize the simulation program were using their experience and intuition to create the designs, and many were not able to logically explain their design at the time of design review by the company.
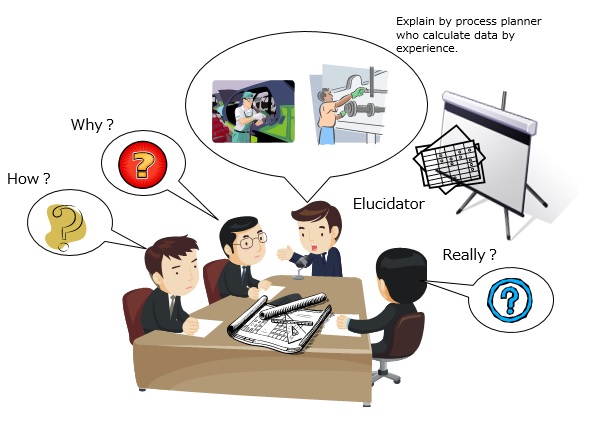
To tackle the problem, GD.findi has the smart production activity control technology. ‘Production activity’ aspect of the production site includes the management of the employees and logistic equipment/tools; these are closely integrated with a production’s cost effectiveness, lead time, stock, and productibility. It is crucial to accurately design these factors. Conventional simulation programs required programmers to script the control settings, requiring program specialists. This time consuming and tedious problem is drastically solved by the GD.findi program as it eliminates the need for the control setting program script.
Introducing the GD.findi’s Production Activity Intelligent Control Function: Production activities (management of the employees and logistic equipment/tools) are the most important and dynamic variables in the product simulation. These processes were difficult define; however, GD.findi developed object groups to separate the production activity characteristics into 3 categories:
-Employee activity
-Logistics/Transport activity
-Tooling activity
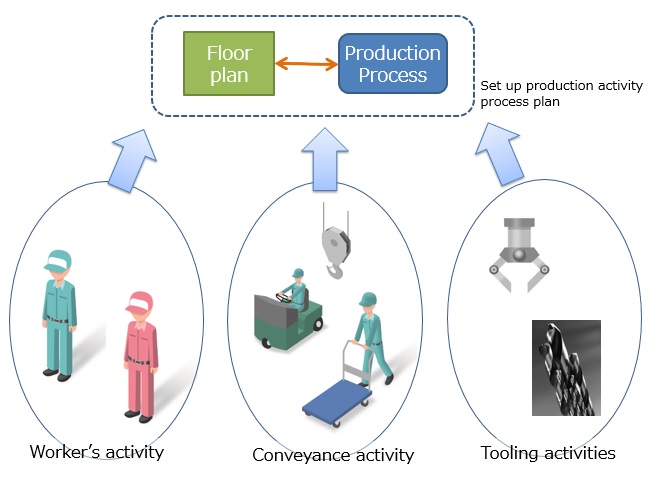
Without these factors, production is impossible. GD.findi program lets users operate the production activities in a simple manner. It is done by assigning the production activities to the defined floor plan and production process. Within those, production activities are to correspond to the tasks assigned to the station. Therefore, users set up the production activities based on the tasks assigned to the station.
Application of the Employee Management
Examine the following example for employee management. A. employee is typically given such tasks:
-In station A, work on the process 3 of product P
-In station A, work on process 2 of product Q
-Employee is in charge of both station A and station
The employee able to work flexibly, and not assigned to work just on a process or a station
In GD.findi, the station assigned to the employee can also be seen as the production activity for the product. Look at the image below, the instructions show how to operate the GD.findi program with an employee with multiple assignments.
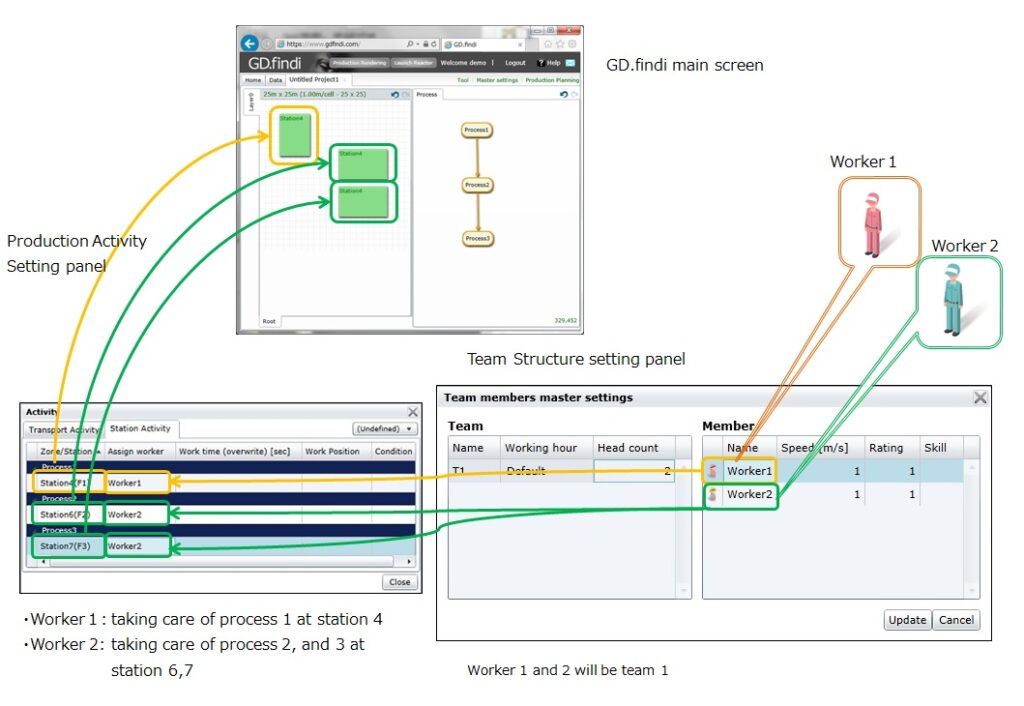
The set up for employees with multiple assignments is done by simply setting the station activity with the employee. When the production activity setting panel is open, one can see the process and its assigned station. For each process, select the employee from the list and assign the person a task. To form a team, open the team member set up panel and select the employees. Users can also input the employee’s name and his/her skill and abilities. With this simple set up, users can easily form a multiple production line and start its production simulation.
Application of the Transport Activity
Next, for the transport, the example shows a production activity that is able to accommodate to situations. Transport activity is not just about repeating its shipment task, it must be able to make accommodations based on shipping destination and shipment timing. Adjustments are made to the shipment timing and its amount for the future shipments from reviewing the previous process. With GD.findi, multiple stations can be assigned similar tasks. In the example, a task is assigned to multiple stations, however, it is conditioned for each station to not be limited to a single task. In addition, short breakdown time in the production line can occur and it must factor the transport time based on the distance between the stations. Thus, as the post process outcome varies, future process shipments must be adjusted based on the production flow. For example, it can be prioritized as:
-Ship from stations with short buffer stock
-Ship from stations with short lead time (high production rate)
-Ship from stations that is closest to the earlier processes
-Make shipments to inhibit stopping of the desired stations (ex. quality products, less breakdown time)
-Ship first from stations that are authorized
-Ship according to the production line order
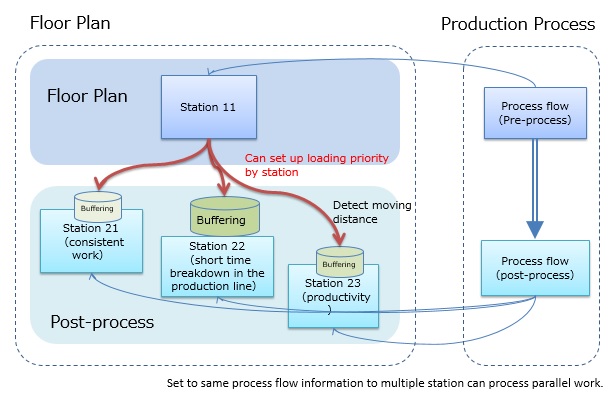
The conventional production simulators require complicated programming script to prioritize the process. Instead, GD.findi can fulfill each production activity by setting its ‘behavioral’ characteristics. In the setting panel of the production activity, the logistic/transport coordinator and ‘behavior’ is selected. For example, the following settings are available:
- FI /First :In Recognize the order of the parts in the buffer.
- NE /Near :Prioritize the station that is closest to the last process.
- LO /Long Cycletime :Prioritize the station with long cycle time
- SH /Short Cycletime :Prioritize the station with short cycle time
- FT /Fixed :Time Ship according to the schedule table
Parameters can be added to the ‘behavior’ to detail its settings. It is impossible to define all the ‘behavior’ that occurs in the production line transport. However, within the process design, users can set the most important ‘behavior’ and its parameters. The main point of transport activity is not the minute details of the control, it is to find the problems that are associated with the productivity and cost of the entire production line. The future research of the ‘behavior’ will show a growth and development in its setting functions.
Application of the Logistic Activity
GD.findi simplifies the logistic design and evaluation which may be a topic many users have interest in. GD.findi places emphasis on the logistics’ ‘passage’ and ‘route’ concept. ‘Passage’ is the information used to prepare the interbay transfers. ‘Route’ is defined as using the path of the ‘passage’ to transfer products from the start to end of the interbay routes. The illustration below shows the two concepts. ‘Route’ is defined by using the parts of ‘passage’.
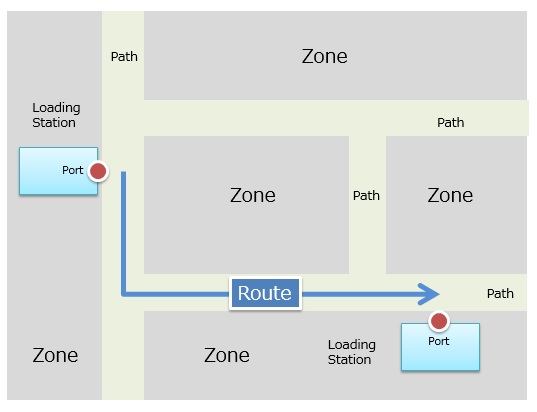
Take a look at the ‘passage’ and ‘route’ defined by GD.findi. The passage is easily set up by the floor plan pane and clicking on the mouse. The ‘route’ setting is not described by the user. It is automatically set by GD.findi using the information on the origin and destination of a transfer. First, it recommends using the shortest distance. However, if the user decides a longer route is necessary, it can be easily selected from the route list created by GD.findi.
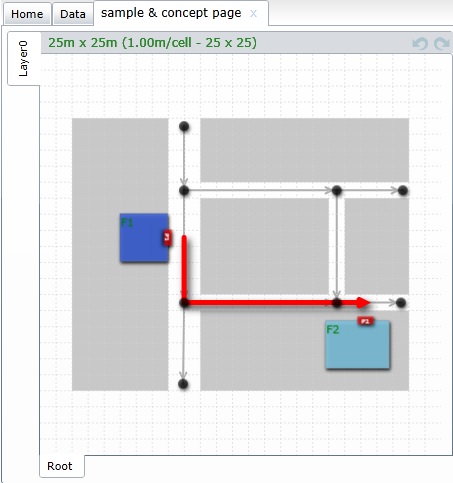
GD.findi has the function to automatically recommend the most suited ‘route’ based on the information obtained from: the floor plan design, transport origin, location of the transfer destination’s station, station to out of station transfer, loading position (port), and utilizing the information on ‘passage’. The program can also automatically choose the best ‘route’ by clicking and dragging, even if the station position, port position, and ‘passage’ are freely changed. Cumbersome definition of a passage setting is unnecessary. Users can create and design their own floor plan without worry since the accommodating passage will be created by the program, which will allow them to avidly evaluate the production logistics.
Optimum Deployment of the Simulation Engine and Cloud Service
GD.findi’s technology is built on simulation engine background. Simulation calculation and its results are obtained by the deployment based internal calculation. The more complicated the data model is, the simulation calculation’s workload increases and requires more time to calculate. GD.findi’s architecture utilizes a specialized mechanism that allows optimal simulation calculation. Even high speed calculation of the grand-scale production simulation can be done with the program. The 3-level architecture: user process mode/mid-code model/run model, yields high speed calculation. In the illustration, user process model is compiled by GD.findi’s mid-code model. The mid-code model is formatted for GD.findi’s simulation engine. It is loaded into the run model at the time of simulation calculation, allowing flawless simulation calculation.
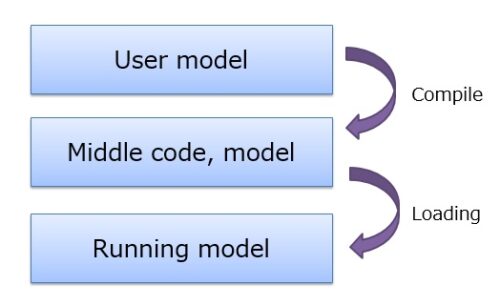
The 3-level architecture and the compatible run model compilation yield results via high speed calculation.
Squeeze (refinement) of a champion plan using simulations
GD.findi’s primary strength is in refinement of potential solution sets without running a large number of conventional production simulations; it runs a single simulation exclusively for verification purposes. Historically, because executing production simulations required extensive preparation a technical barrier existed preventing facility layout problems from being solved.
In GD.findi, it is possible to refine plans while specifying loose initial constraints. This allows it to construct an initial solution space while plans are still being finalized.
Take for example the tooling plan for a facility. Some initial conditions such as molds and machinery can be specified initially, and other constraints such as transportation methods and worker assignments can be added at a later point in time.
On the other hand, state conditions such as manufacturing cost and inter-process inventory can be determined with limited constrains. By using such conditions with performance metrics like lead time and capacity utilization of potential solutions, the viable set of solutions can be narrowed down by modification of the plan.
This approach can be summarized as generating a pool of early-stage plan candidates, and by adding constraints selecting a “champion” plan. At each iteration of the M x N simulation, a condition is added and the pool narrows. As such, this process is termed “squeeze simulation”.
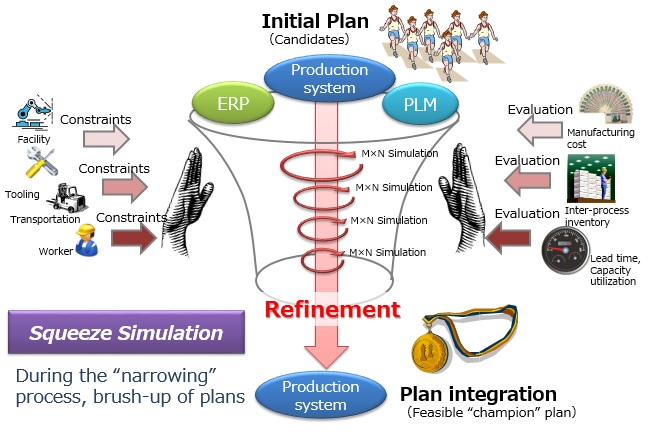
For product information about GD.findi MS, a production system simulator that utilizes GD.findi Data Model, please click the following button.